Complex Optimization Process in 4 Steps
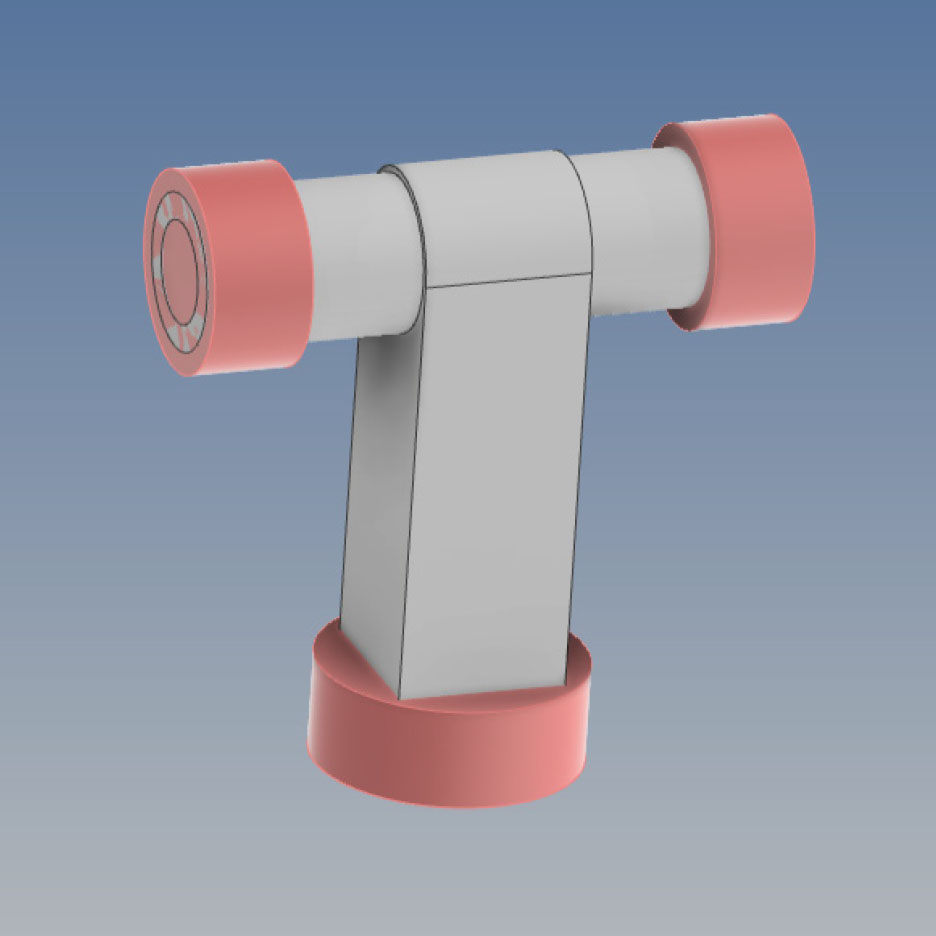
1.
Easily Define Loads and Supports in Your CAD System with Superficialis
Before beginning the simulation process, Superficialis makes it easy to define loads and supports directly within your CAD system. This streamlined approach saves time and effort, allowing you to focus on optimizing the performance of your designs.

2.
Seamless Shape and Topology Optimization with Superficialis
Once you’ve sent your simulation model to Superficialis, our system automatically initiates the optimization process. This streamlined approach saves you time and effort, so you can focus on optimizing the performance of your designs.

3.
Preview and Prepare Your Optimized Structures for Additive Manufacturing with Superficialis
With Superficialis, you can preview the result of your optimization process and prepare your structures for additive manufacturing. Our software makes it easy to take your designs from concept to reality, ensuring that your structures are optimized for performance and ready for 3D printing.

4.
Shortcut to Optimal Solutions with 3D Printed Parts and Superficialis
Streamline your design process and achieve optimal solutions faster with Superficialis and 3D printed parts. Our software makes it easy to optimize shape, topology, and lightweight structures for additive manufacturing, ensuring that your designs are ready for 3D printing and optimized for performance.
Optimization Process - Example
Selected Results
Bellcrank
Bellcrank model made of 2014A-T6 optimized in Superficilis software, reducing amount of used material by 68% without compromising part safety even in the most critical load cases

CAD design Biomimetic optimized element
Control arm
Front control arm model made out of 6061A-T6 optimized in Superficilis software, reducing used material by 53% without compromising stiffness of the construction.

CAD design Biomimetic optimized element
Steering knuckle
Optimization of element made out of special aluminum alloy AA7075 for minimal mass with stress constraint ensuring adequate stiffness despite the significantly reduced material volume.

CAD design Biomimetic optimized element
Head of scooter
Scooter head made out of steel s316L optimized with main goal of reducing elements mass and adapting geometry to 3D printing.

CAD design Biomimetic optimized element
lightweight structures
A lightweight design holds significant importance, particularly in automotive and aerospace industries. By minimizing weight, there is a natural reduction in dynamic forces, yielding various advantages such as decreased energy/fuel consumption in vehicles or equipment. This streamlined approach also simplifies component handling and ensures compliance with weight requirements in highly demanding applications.
improved performance under changing conditions
Real-world applications of structural elements are often more intricate than the textbook examples in mechanics. Our system excels at translating even the most complex load cases into results of unquestionable quality.
resistance and durability
We thrive in situations where exceptional component performance is crucial, not only in achieving lightweight designs but also in ensuring robust strength and adaptability to the most demanding applications. Our capability extends beyond weight reduction; we can simultaneously enhance mass while creating unique geometries tailored to withstand even the most extreme loads.
material specific approach
Is it necessary to manufacture the same part, whether in steel or aluminum, identically? We advocate for distinct optimization approaches tailored to each material. Our capability lies in deriving varied results based on different material parameters, whether they involve specialized properties or commonly used construction materials.